钠基膨润土在粘土砂中的作用及变化
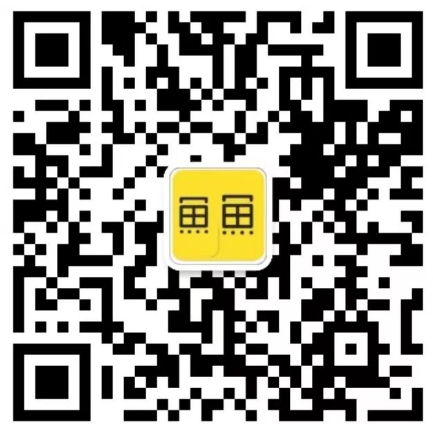
添加微信好友。 免费测试。
复制微信号
铸造用膨润土主要有两种:钠膨润土和钙钠膨润土。 钠基膨润土是由天然钠基膨润土或人造钠基膨润土加工而成。 它以其良好的可重复使用性和较高的湿压强度而在铸造行业中受到欢迎。 由于其良好的塑性,可以防止铸件中的夹砂、结疤、掉块、砂型崩模等现象。 此外,其成形性强、型腔强度高,方便金属工业铸造湿式或干式模具,成为精密铸件的首选。 型砂粘合剂。 钙钠膨润土由天然钙钠膨润土加工而成,是轻质铸件常用的型砂粘结剂。 以其实用性、铸件清砂方便等特点深受用户欢迎。
与其他粘结剂相比,膨润土有一个重要的特点,那就是它具有一定的耐热性。 只要加热温度不太高,除去游离水的膨润土仍然可以通过加水恢复其粘结能力。 膨润土的粘结能力只有加水后才能表现出来。 膨润土失去结合能力也与其脱水有关。 到目前为止,人们认为膨润土中的水存在三种形式:一类水是游离水,即被膨润土颗粒吸附的水。 当加热至100℃以上时,可除去游离水。 除去游离水的膨润土粘结能力较差。 不受影响; 这两种水都是牢固结合水。 当在110℃长时间加热时,膨润土可以完全除去游离水,但不会除去牢固结合的水。 完全除去游离水的膨润土在较高温度(如200℃、300℃)加热时会继续失重,说明仍有失水现象。 膨润土经这样加热脱水后,只要加水即可完全恢复粘结能力; 这三种水都是晶格水,又称结构水。 在相对较高的温度下只能部分或完全去除晶格水。 膨润土的晶格水除去后,就失去粘结能力,成为死粘土。
不同的膨润土在不同的温度下失去粘合能力。 差热分析实验证明:一般来说,天然钠膨润土的失效温度为638℃,钙膨润土的失效温度为316℃。 人工活化钠膨润土因活化条件不同,失效温度也不同,但均低于天然钠膨润土。 可见,粘土砂中的膨润土有两种类型,一种是有效膨润土,一种是死粘土。 死粘土越多,粘土与沙子的结合力就越差。
当钠膨润土加热到600℃以下时,其粘结能力基本不受影响。 当加热温度超过600℃时,粘合能力迅速丧失。 当加热到700°C以上时,粘合能力几乎完全丧失。 钙膨润土在100℃以上开始慢慢失去其粘合能力。 加热温度越高,粘合能力的损失越明显。 首次使用人工活化较差的钠基膨润土时,其失效温度仅略低于天然钠基膨润土。 反复加热数次后,变得与钙膨润土相似。
当熔融金属注入铸型时,靠近铸件表面的型砂被加热到800℃以上(有些有色合金达不到这个温度)。 无论你使用哪种膨润土,型砂这部分的膨润土都会变成死粘土。 这些死粘土有的随型砂附着在铸件表面并被铸件带走,而有的则残留在回收的旧砂中。 除了制造大型铸件外,大多数型砂在铸造过程中都达不到这样的温度。 但由于不同的铸造厂家采用不同厂家生产的膨润土,去除晶格水的温度不同,去除晶格水的速率也不同。 如果使用可以轻松去除晶格水的膨润土,即使在不直接靠近铸件的型砂中,更多的膨润土也会失效并变成死粘土。 如果使用不易除去晶格水的粘土,则会产生较少的死粘土。 总之,膨润土添加量越少越好。 粘土砂中有效膨润土含量越高,膨润土因热而失效的情况就越多。
老治沙
用粘土湿型砂造型铸造后,除靠近铸件部分型砂中的活性膨润土因受热失效而成为死粘土外,大部分型砂可回收利用。 配制粘土湿砂时,旧砂用量一般在90%以上。 如果旧砂处理不当,无论如何加强混砂,无论添加什么辅助材料,都得不到好的型砂。 因此,对旧砂进行有效处理是保证型砂质量的前提。
为保证型砂性能稳定,旧砂温度应保持在50℃以下。 如果超过50°C,则被认为是热沙。 热砂问题已被公认为粘土湿型砂铸造必须面临的最大问题。 型砂温度过高,铸件容易出现夹砂、表面粗糙、冲砂、气孔等缺陷。 目前型砂冷却装置的品种和规格较多,有冷却滚筒、双盘冷却器和冷却沸腾床等,它们都是利用水蒸发来冷却型砂。 其中,冷却沸腾床效果较好。
严格控制旧砂的含水率非常重要。 如果进入混砂的旧砂含水率过低,对混砂质量的影响可能不亚于砂温过高。 铸型浇注后,由于铁水的影响,许多砂粒表面的土水结合膜脱水、干燥。 加水吸收水分并恢复可塑性并不容易。 旧砂的含水量越低,加水并在混砂机中混合以达到所需性能所需的时间就越长。 由于生产中混砂的时间有限,旧砂的含水率越低,混砂的整体质量越差。 进入混砂机的旧砂的水分只能比混砂的水分稍低。 这样,砂子冷却到进入混砂机之间还有很长的时间,水可以充分润湿旧砂粒表面的膨润土。
对于用粘土湿型砂制造的铸铁件,型砂的粒度应更细。 由于混砂时旧砂的用量一般在90%以上,因此决定型砂粒度的主要因素是旧砂。 新砂的添加量很少,不可能通过添加新砂来改变型砂的粒径。 因此,应经常检查旧砂的粒度:140目筛上的砂应在10%~15%之间,200目筛、270目筛及底盘上的细砂之和应为尽可能少,细砂总和一般应小于4%。 吸水细粉的含量最好控制在2%~5%之间。 如果吸水细粉含量过高,则型砂含水率较高,易导致铸件出现针孔、表面粗糙、砂眼等缺陷。 ; 如果吸水细粉含量太低,型砂的性能(特别是压实性)不稳定。 吸水细粉主要是死粘土,也包括焦煤颗粒和其他细粉。
膨润土添加量
混砂时必须加入一定量的膨润土,使型砂中保持必要量的膨润土。 膨润土的含量通常采用亚甲蓝法测定。 用亚甲蓝法测得的膨润土量称为有效膨润土量。
新加入砂量
新砂加入量不宜过多,以保持系统内砂总量稳定。 添加过多的新砂会对型砂的质量产生负面影响。 我国铸造厂普遍存在大量散砂,不少工厂新砂添加量为5%~8%。 当然,新砂的加入量还必须考虑设备条件、芯砂进入量等诸多因素。
煤粉补充量
煤粉的添加量必须根据旧砂中有效煤粉的测定值来确定。 粘土湿砂中煤粉含量一般应控制在3.5%~5.5%之间。 当然,煤粉的添加量必须根据铸件的特性和煤粉的质量来确定。
拌沙
混砂的主要作用是将粘土砂中的各组分混合均匀,使水充分润湿膨润土,使有效的膨润土膏体涂覆在砂粒表面。 目标是使粘土砂适应造型设备的性能。 由于膨润土膏体是半固体粘性材料,因此需要大量的能量才能达到上述目的。 如果混砂设备的功率不高,或者混砂时间不够,膨润土就不能充分发挥其粘结作用,型砂的强度不高,其他性能也不高。乖一点。 如果提高型砂中的水分,提高膨润土膏体的含水率,降低膨润土膏体的粘度,就可以减少涂覆膨润土膏体所需的能量,即可以缩短混砂时间。 但由于膨润土膏体的粘度降低,型砂的湿压强度也急剧降低。 这种方法其实并不可取。
为了减少混砂所需的能量,采用合理的加料顺序很重要。 拌旧砂时,不要按惯例先加入干料(沙子和膨润土),干拌一段时间,然后加水拌匀。 应先加入沙子和水并充分混合,然后加入膨润土,因为水已经分散,没有较大的水滴。 添加膨润土后,只能形成大量较小的粘土球。 压开这些小粘土球更容易,并且需要更少的能量。 也就是说,使用相同的混砂设备获得相同质量的型砂需要更短的混砂时间。 国外一些铸造厂在使用间歇式混砂机时,混砂前先向混砂机内加水并运行几秒钟(当然设备要保证水不漏)。 这样,不仅具有上述先加水的好处,而且可以在每次混砂前清洗砂轮和刮刀,提高混砂效率。
湿压强度
湿压强度的控制目标必须根据建模方法来选择,绝不是高强度。 型砂的强度越高,造型时捣碎所需的能量就越大。 现在很多铸造厂的型砂强度过高。 有些用于手工造型或振动机造型的型砂湿压强度高达130~。 用这样的型砂很难将铸型捣得很紧。 其结果是铸件表面质量不好,容易出现缩松缺陷。